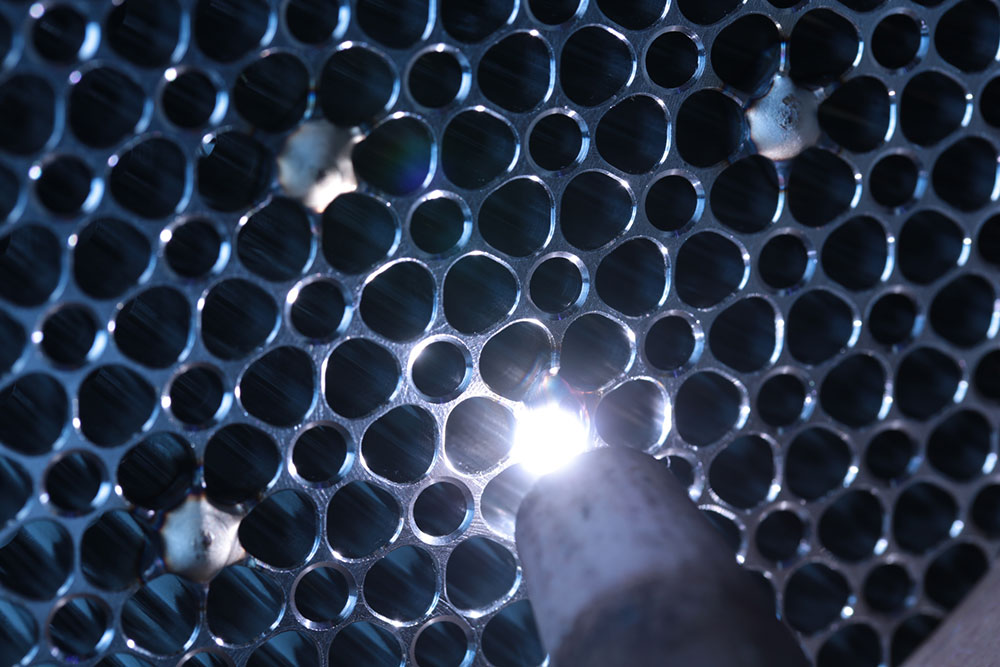
Changes in organizational structures made by TVEL Fuel Company are stipulated by structures formation based on target programs, objectives and strategy of TVEL Fuel Company. This approach is in line with the industry-wide standards, and was adopted within implementation of the project of Rosatom for harmonization of the organizational structure of the companies comprising the industry. The ultimate goal of these transformations is to establish functional chains of Rosatom – TVEL JSC – subsidiary company, to enhance the efficient interaction between the management levels within TVEL Fuel Company and to cut the red tape.
In 2017, TVEL Fuel Company focused on the implementation of the strategic goal for development of the second core of business - formation of a mechanism for managing the creation of new non-nuclear products and their promotion to the market. Within the framework of this direction, there have been changes in the organizational structure of TVEL Fuel Company with the aim of creating a more effective system for managing the development, production and sale of products of general industrial activity.
TVEL Fuel Company carries out organizational works to develop services on Nuclear and Radiation Hazardous Facilities (NRHF) decommissioning as a new business.
In 2018, SGChE JSC, AECC JSC, CPTI JSC and VNIINM JSC have launched the process of forming competence centers for decommissioning nuclear and radiation hazardous facilities. The main goal of these centers is to perform works on NRHF decommissioning with their own resources both on their sites and in Russia, and abroad.
This area will allow TVEL Fuel Company not only to provide economic benefits, but also to create new jobs.
PRODUCTION SUPPORT OFFICE FUNCTIONS
The Company’s enterprises continued to improvethe efficiency of production support office functions.
One of the key projects 2018 “Production planning with the supply chain” had the following results:
- reduced planning process lead time from an application to the formation of production sites plans by 25.3%;
- “right on time production according to volumes and nomenclature” indicator was recorded at 82.7% in MSZ PJSC, NCCP PJSC, Centrotech SPA LLC, ChMP JSC.
In 2018, within the framework of the industry project “Branch Topology Concept” the Company successfully implemented the program “Increasing the efficiency of areas use in TVEL Fuel Company”. In the reporting period the Company’s enterprises developed, within the framework of this program, the concepts of sites development, 9 of which were approved by the Governing Board of TVEL Fuel Company.
According to the results of this program, the Company managed to reduce buildings area for more than 200 thousand sq. m, while reducing the costs for maintenance and operation for more than RUB 300 mln. The Investment Committee of TVEL JSC approved the implementation of the 7 “first wave” compaction projects. 10 compaction projects more are planned in 2019.
83% of personnel participate in the improvement process through SFI submission. For each employee of the Company has an average of 5.6 SFI. Among the Company’s enterprises AECC JSC (over 13 SFIs) and SGChE JSC (over 12 SFIs) have the highest number of SFIs per employee. Most of SFIs are aimed at improving the conditions and ensuring occupational safety. Economic benefit from SFI and efficiency suggestions implementation made RUB 263.8 mln in 2018.
The sites development concept of TVEL Fuel Company is constantly updated and refined in terms of cost-cutting and implementation of compaction projects. The term of the program accomplishment is till 2022.
The results of launching the production in vacant facilities by TVEL Fuel Company in 2018:
- UEIP JSC: signing of a lease agreement for a building of 1.400 sq. m. area in the city (not within the industrial site) with Novouralsk Pipe Plant LLC for the production of HDP pipes for water, gas and cable laying. 10 new jobs were created.
- ChMP JSC: use of vacant site of 50 square meters in the existing production building No. 50 for a new business area - production of hafnium iodide powder. 2 additional jobs were created for operation of the site.
- KMZ PJSC: as part of the relocation of special purpose equipment to Tochmash VPA JSC the Company rented 13.131 sq. m of production area and 496 sq. m of office area. 166 new jobs were created.
KMZ PJSC COMPLETED THE COMPACTION PROCESS FOR GAS CENTRIFUGES
TVEL Fuel Company implements a large project on concentration of all mechanical production facilities in Vladimir region at KMZ PJSC with the transition of the corresponding facilities and personnel from Tochmash VPA JSC (Vladimir). Tochmash VPA JSC, in its turn, plans the development of non-nuclear production and attraction of external resident investors to its production site. By optimizing production space and reducing energy consumption, the fixed costs of the two companies are planned to be almost halved by 2019.
Thus, the final stage of the investment project “New facility for gas centrifuges production” was completed in 2018. The project implementation included a set of measures, such as concentrating the production of gas centrifuges in one building, purchasing modern high-performance equipment, launching mass production of gas centrifuges of new generations, increasing the level of automation and the quality of output products.
It resulted in achievement of a key indicator - reducing the cost of production by reducing the work in progress and the lead time of production processes due to the concentration of production in one building (before its start, the production of gas centrifuges was located in four buildings). Moreover, the company managed to reduce its production space more than twice - from 151.1 thousand sq. m to 71.6 thousand sq. m. The reduction of production costs was also due to the R&D results obtained by TVEL Fuel Company in the field of gas centrifuges of new generations.
BUSINESS PROCESS DIGITALIZATION
With the view to increase the efficiency and optimize business processes, TVEL Fuel Company uses up-to-date information technologies (IT) and solutions.
In July 2018, TVEL Fuel Company approved the IT strategy for 2018-2023 in terms of process digitalization. The strategy provides for the implementation of 135 information technology projects in 8 areas of development. Deadlines, budget and internal business customers are determined for each project.
Creation of digital production takes the central place in the strategy. Maximum use of information technologies will allow the enterprises of the Fuel Company to move to a new way of organizing their production activities. Simulation modelling will help to create digital models of existing or projected production, which will give the opportunity to choose the optimal layout and composition of equipment, and to build the ideal production flows.
Another key objective is to integrate the enterprises of the Fuel Company, representing various industrial processes and links in the production chain, into the Unified digital platform for product life cycle management, and to create a digital interaction ecosystem for developers and partners. The engineering data management system will allow to switch to the work with a product’s “digital twin” (software analogue of a physical device, simulating internal processes, technical characteristics and behavior of a real object under external influence conditions) throughout the product life cycle, and to use uniform product data by all participants from developers to operation support experts.
The important objectives also include the implementation of operational production management systems and the automation of maintenance and repair of production equipment, which will ensure a steady increase in labor productivity and a reduction in costs per production unit.
IT infrastructure development projects of TVEL Fuel Company are intended, specifically, to create a hyper-convergent environment in data processing centers, supporting the implementation of Big Data technologies, and to build up an infrastructure of virtual workplaces.
In October 2018, the Company approved the strategy of information technologies development subject to products areas. The implementation of this strategy will allow to commercialize the Company’s developments in the field of information technologies and create an additional synergistic effect with the internal digitalization strategy of TVEL Fuel Company. The following is offered to foreign markets:
- simulation modelling services and BIM design of industrial facilities;
- predictive analytics solutions for big data processing;
- solutions for robotization and intelligent data processing;
- production of network equipment.
Major IT projects implemented in 2018
Project “Development of subsystems for intelligent information processing and robotization of user activity as part of the project for automating the process of preparing a set of procurement documents (pilot)”
In 2018, the basic implementation of the subsystems was completed - the project moved to the stage of pilot production. The solution is being tested by the servicing department which is responsible for preparing (including through the new system) procurement procedures.
The intellectual processing system for information has been set up and trained on real examples: it already knows how to check technical specifications according to the rules, as well as to extract parameters from suppliers' technical and commercial proposals, which are necessary for the formation of nominal (maximum) contract price. The main objectives for stabilizing the system’s work, which are now being addressed by the project team, are to adjust the system’s response to experts’ comments and to work out new validation rules arising during pilot operation.
Within the robotization subsystem, seven software robots have been developed that perform the functions of searching for price sources and target requests for technical-commercial proposals.
The immediate goal of the project is to launch permanent operation of the solution and stabilize it, and to prioritize the objectives of the system further development in 2019. The Information Technology Department plans to promote the product both within the subsidiaries of TVEL Fuel Company, and within other industry-specific enterprises.
Project “Automation of the process of registration of billing and invoice documents (pilot)”
In December 2018, TVEL Fuel Company completed the creation of a system that allows to qualitatively recognize scan images of primary documents and extract the attributes necessary for their further use in problem solving by the SAP ERP system. The next steps include the system’s transfer into pilot operation, and a set of improvements in SAP ERP of TVEL Fuel Company for the automated formation of reservations of funds and payment schedules based on the information of primary accounting documents.
Project “Typical functionality pilot implementation for Equipment Maintenance and Repair based on SAP ERP in UEIP and ChMP”
The project to create typical functionality of Equipment Maintenance and Repair in SAP ERP system of the Fuel Company was started in July 2018 with ambitious deadlines - five months for solution design, accomplishment and preparation for launching the commercial operation. TVEL Fuel Company’s SAP for Equipment Maintenance and Repair was put into commercial operation in December 2018 in UEIP JSC, ChMP JSC and TVEL JSC.
Till the end of April, a period of the system stabilization is planned, during which the users will receive support and optimize the processes based on the feedback from experts of TVEL JSC enterprises.
Objectives of the project include the automation of planning processes and recording of repairs, the integration of Maintenance and Repair processes in TVEL Fuel Company’s enterprises based on the unified information system SAP ERP, which will help to make procurement of spare parts, services for repairs and the process of recording and analysing maintenance costs for the Equipment Maintenance and Repair transparent and unified.
In the first quarter of 2019, ChMP JSC implemented the integration of Equipment Maintenance and Repair system with the production management enterprise system (MES) in order to minimize the impact of equipment downtime on the implementation of the production program by the enterprise. Plans for 2019 include start of the introduction of mobile repair control technologies for increased convenience and equipment inspections control. And the final step, the introduction of predictive analytic tools is planned which will provide the greatest effects in the form of reduced operating costs for Equipment Maintenance and Repair and improved availability of the equipment. Thus, in three or four years, the Fuel Company will have an integrated digital solution for Equipment Maintenance and Repair control.
Project “Creation of a project and program management system”
In the second half of 2018, the Company carried out the works to collect, analyse and formalize the requirements for automation of project management processes, in which the experts from all divisions responsible for project activities took an active part. As part of an industry-specific project management maturity program, TVEL JSC plans to create a Project Management Information System.
Project “Legally binding electronic document flow”
In 2018, the constant (industrial) operation of electronic documents exchange process has started within the framework of TVEL Fuel Company’s target accounting systems SAP ERP and 1С ERP:Rosatom between the enterprises of Rosatom State Corporation included into the organizational perimeter of the project (104 enterprises). The transition to legally binding electronic document flow allowed to abandon paper originals. Electronic documents have full legal force: they can be sent to a court and tax authorities, used as a basis for obtaining a VAT deduction. The documents exchange is carried out through a licensed operator guaranteeing the security of transmitted information.
Project “Introduction of basic MES functionality”
In 2018, NCCP PJSC launched the pilot project and developed design specifications for creating a production management enterprise system (MES). The system is designed to automate the processes of operational control and production of FA for power reactors and their components in sections 1, 3 and 4 of shop No.10 of the Novosibirsk Chemical Concentrates Plant (NCCP PJSC). The main objectives of MES are to increase the efficiency of production accounting, ensure control and traceability of production throughout the production cycle, and reduce labor costs through automated generation of production reporting. The Company plans to carry out technical design and implementation in 2019, testing and commissioning of the system in NCCP PJSC will be carried out in the 2nd quarter of 2020. In 2020, MES development within ChMP JSC will be continued as well, and MES implementation project will be initiated in MSZ PJSC.
Project “Replication of Laboratory Information System in MSZ PJSC”
MSZ PJSC has developed design specifications for creating the Laboratory Information System (LIMS) and now is preparing to start the project. The system is designed to automate the processes of collecting, processing, accumulating, storing and displaying the information obtained as a result of non-destructive testing to determine the quality of semi-finished and finished products. The main goals of LIMS creating are to optimize loading of personnel involved in laboratory control processes, to reduce the duration of the production cycle through the use of automated planning tools, processing of test and accounting results. Technical design of the system will be carried out in 2019, commissioning is scheduled for 2020.
Project “Creating an experimental and engineering data management system for VNIINM”
Technical design has been completed and the implementation of the system has begun. The system is designed to automate the development and management of scientific and technical documentation, design, technological and other technical documentation, experimental and engineering data, ensuring electronic interaction of VNIINM JSC with ChMP JSC, MSZ PJSC and TVEL JSC. Commissioning is scheduled for the beginning of the 3rd quarter of 2019. Additionally, as part of the production concentration project in KMZ PJSC and Tochmash VPA JSC, the Company plans to complete works on the integration of the Automated Control System for Design Engineering Pre-production of these enterprises, to implement automated rationing and to ensure the integration to SAP ERP of TVEL Fuel Company in 2019.